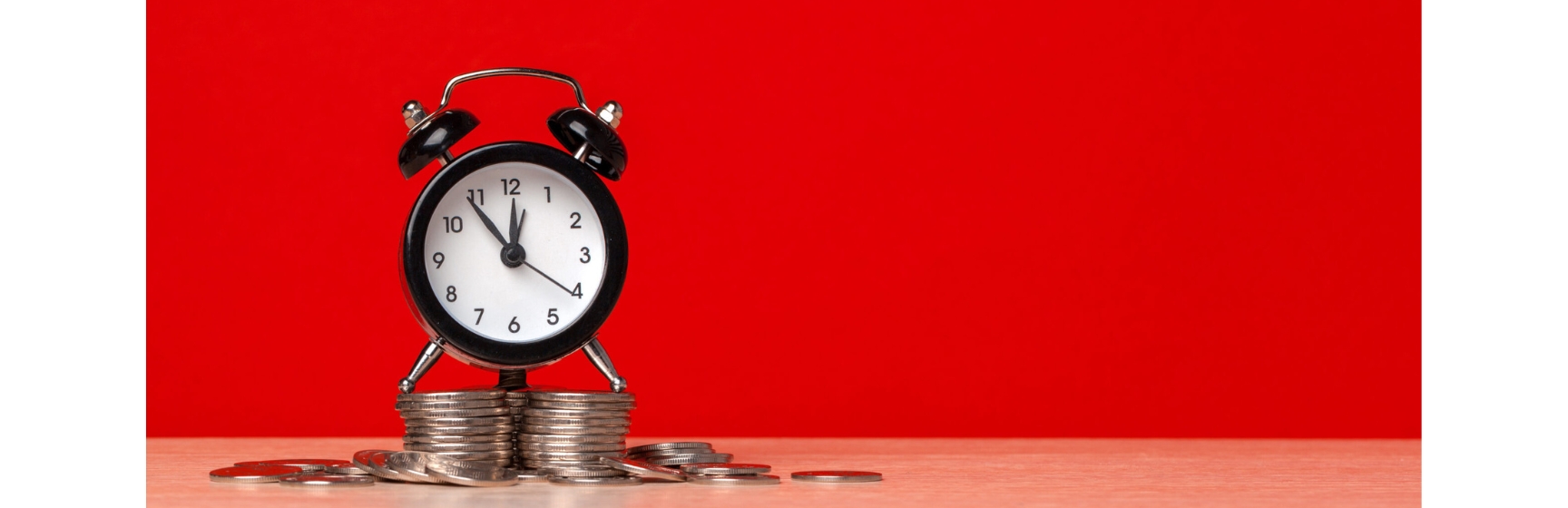
By Vilmer Ståhle
3 minute read
Vilmer Ståhle By Vilmer Ståhle
3 minute read
When considering investing in a PLM (Product Lifecycle Management) solution, it's crucial to assess the current processes in place and the potential costs of not having a PLM system.
By choosing the right PLM solution, businesses can experience significant improvements in time to market, cost reduction, productivity acceleration, and overall operational savings of up to 30%.
To accurately determine the costs associated with outdated procedures, it's essential to identify the processes that generate expenses when a company does not utilize a PLM system.
Cost-Generating Processes
- Managing product data through numerous Excel sheets becomes challenging, hindering team alignment with the latest information.
- Redundant information processing across departments is time-consuming, resulting in delays and extended time to market.
- Searching for information in employees' local folders wastes time and slows down workflows due to restricted access, hindering efficient knowledge sharing.
- Data errors are prevalent and can lead to significant business problems, such as ordering the wrong materials or failing to meet minimum order quantities.
- Communicating with suppliers via email creates workflow bottlenecks, impeding efficient collaboration.
- Excessive administrative tasks limit team productivity, leaving less time for core responsibilities and stifling creativity.
- Marketplaces and e-commerce platforms require product and marketing data in specific formats, causing time-consuming efforts to deliver and format the data according to their requirements.
- Inaccurate communication of tech packs leads to supplier miscommunication, costly errors, and additional work.
Sometimes, the need for a PLM may not be apparent due to a lack of data on the actual cost of not having a PLM solution. To address this, let's quantify the costs associated with current processes.
Calculating the Costs of Not Having a PLM
To estimate the costs accurately and evaluate the benefits of investing in a PLM solution, follow these steps:
-
Determine the number of hours spent annually per employee on the following activities
- Searching through emails for specific information
- Tracking the latest updated Excel sheets
- Rectifying information errors
- Preparing reports
- Communicating with suppliers via email
- Dealing with paperwork and organizing information
- Sharing redundant information across departments
- Fixing mistakes caused by inaccurate communication of tech packs
-
Engage design, sourcing, technicians, and back-office teams to quantify these time expenditures. A rough estimate will suffice.
The sum of hours spent on these tasks represents the annual number of wasted hours.
Example
Two technicians estimate wasting 6 hours per week, while three designers report wasting around 6-8 hours each week. A rough estimate would be 7 hours per week, multiplied by 40 weeks a year, resulting in 280 hours wasted per employee annually.
-
Calculate the value of one hour
- Divide the average employee's salary by the annual number of working hours to determine the hourly rate cost.
Example
Assuming the average monthly salary is €4,500, and the monthly work hours are 160, the hourly rate cost would be €28.
-
Quantify the value of wasted hours
- Multiply the annual number of wasted hours by the hourly rate cost to determine the cost per employee.
Example
280 wasted hours multiplied by €28 per hour equals €7,840 wasted per employee.
-
Calculate the total cost
- Multiply the cost per employee by the number of applicable employees to obtain the overall cost.
Example
If five employees each waste hours worth €7,840, the total waste amounts to €39,200 per year, encompassing activities such as searching for information and ensuring up-to-date work processes.
Generate Operational Savings with a PLM
Implementing a PLM platform eliminates the cost-generating activities mentioned above, providing efficient tools to manage these aspects.
While there are numerous benefits of utilizing a PLM system, evaluating the cost-generating activities can help determine if investing in a PLM is a viable business case. Typically, companies achieve operational savings of up to 30% of their overall operational costs by implementing the right PLM solution.
Example
Based on the previous example with five employees, a PLM platform can potentially improve their efficiency by an annual value of €39,200. Implementing a PLM platform for five employees can cost as little as €10,000 per year, which is less than 25% of the value of the efficiency improvement.
Numbers provide valuable insights. Schedule a demo consultation with us, and together, we can assess your current processes and analyze whether investing in a PLM solution will yield a profitable business case for your company.